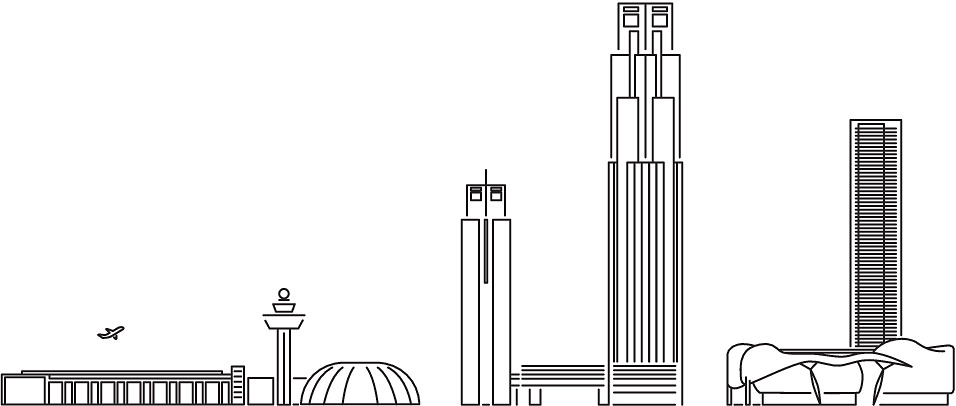
Singapore
The A-Team
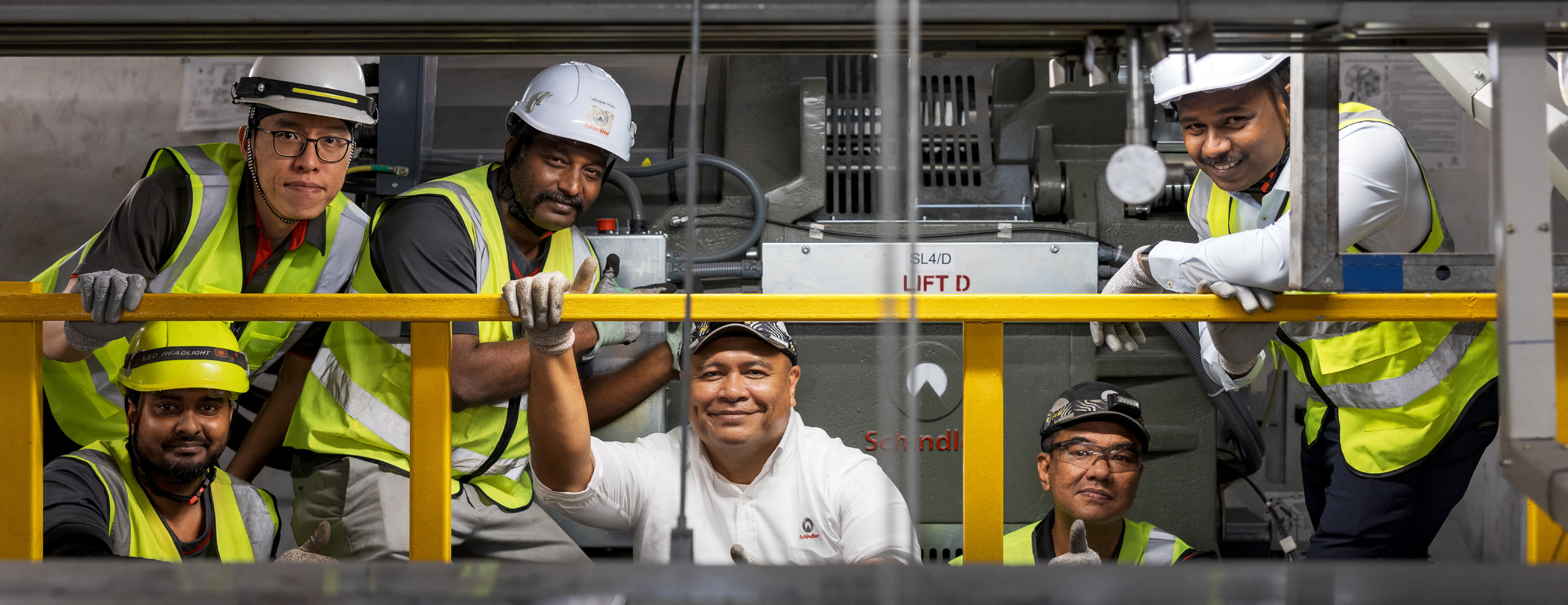
Installations, maintenance, repairs, and modernization projects – they do it all. Several hundred Schindler employees work hard each day to ensure that everything runs smoothly in Singapore.
Loh Hui Yi stands on an escalator, letting the handrails glide beneath her fingers. With intense concentration, she inspects the handrails for small cracks or bumps in the plastic. In the background, announcements for flights to destinations across the globe echo through Changi Airport. Each year, around 60 million people pass through this hub connecting Europe, Asia, and Oceania. Laden with suitcases and backpacks, they land in Changi Airport or prepare to depart for far-off destinations, all relying – often without even realizing it – on escalators, elevators, and moving walks to get them and their luggage safely and swiftly through the airport.
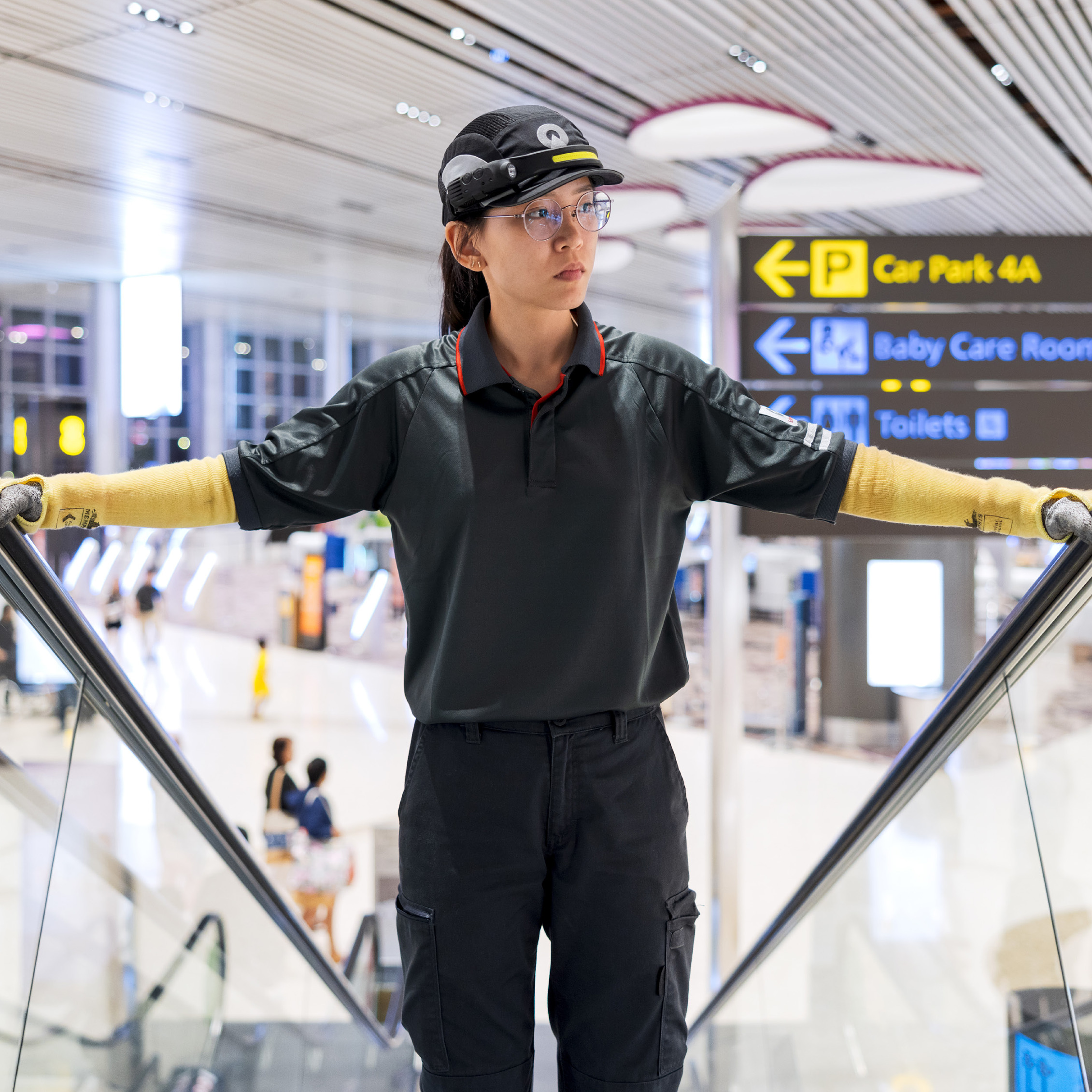
It’s late in the evening, but Loh Hui Yi and two service technicians are ready to service the 87 Schindler units in Terminal 4. The young electrical engineer is not a permanent member of the service crew: she’s currently completing the Field Engineer Development Program (FEDP) and is on a work placement at Changi Airport. Schindler’s two-year FEDP fosters young talent, teaching them about the latest products and technologies while training them to become qualified technicians. Mentors supervise their work on-site and provide coaching. “Before I joined Schindler, I worked in the car sector. I knew very little about the elevator industry,” says Loh Hui Yi. “Since starting the FEDP, it’s been a steep learning curve but I’m really enjoying it.”
Toh Jia Yue, Service Manager Major Projects, is convinced that Schindler’s training and development strategy delivers results: “We place great importance on employee training. Our customers are very demanding, and the local market is fiercely competitive, so having qualified professionals is vital.”
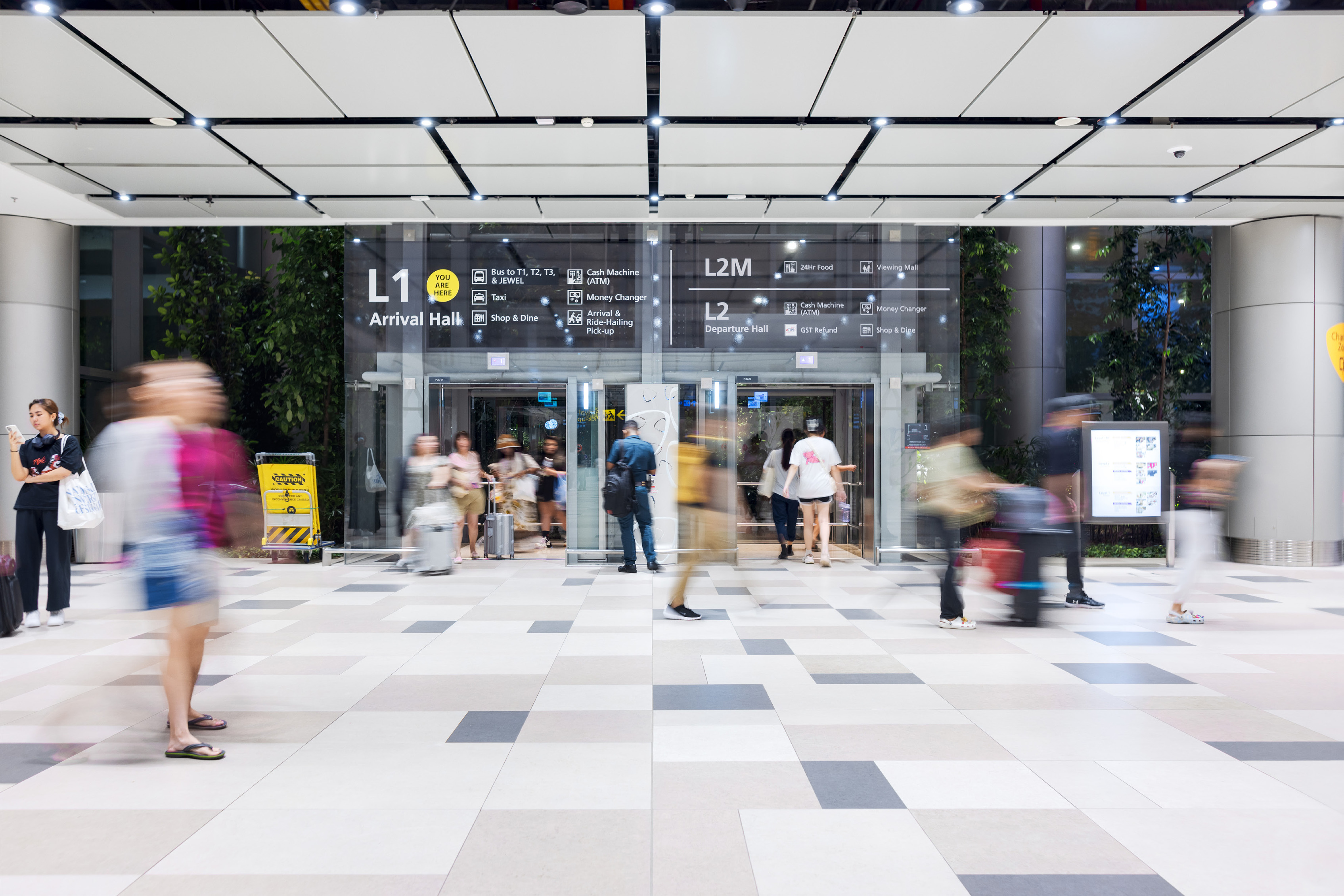
The airport team is just one of the countless crews working tirelessly – at night or behind the scenes during the day – to maintain and repair Schindler elevators, escalators, and moving walks. Their primary focus is on maintaining and protecting the installations to ensure maximum performance for many years. They work to keep the equipment operating safely and without interruption, extending its lifetime and preserving its quality and value. When necessary, the service professionals can tap into the collective intelligence of more than 40 000 Schindler service technicians and engineers worldwide, whose expertise is stored in a global knowledge base. And, depending on the maintenance contract and type of installation, smart digital tools may also come into play. These “cubes” connect the equipment to the cloud, reporting even the smallest of errors to the Technical Operations Center, where they can often be resolved remotely. This technology reduces the number of breakdowns, resulting in extended operating hours and reduced downtime for building managers and owners.
In the luxury shopping mall ION Orchard, two high-rise elevators are already connected to the cloud, and are being monitored in real time by the Technical Operations Center 16 kilometers away. The remaining 54 Schindler units in the shopping mall are checked manually by Quek Ngee Song, according to a fixed maintenance schedule. “The elevators and escalators in public buildings like these are used much more intensively than those in residential buildings. We therefore carry out checks on them much more frequently,” explains the service technician. He’s been at Schindler for three years and enjoys working in such a pleasant environment as ION.
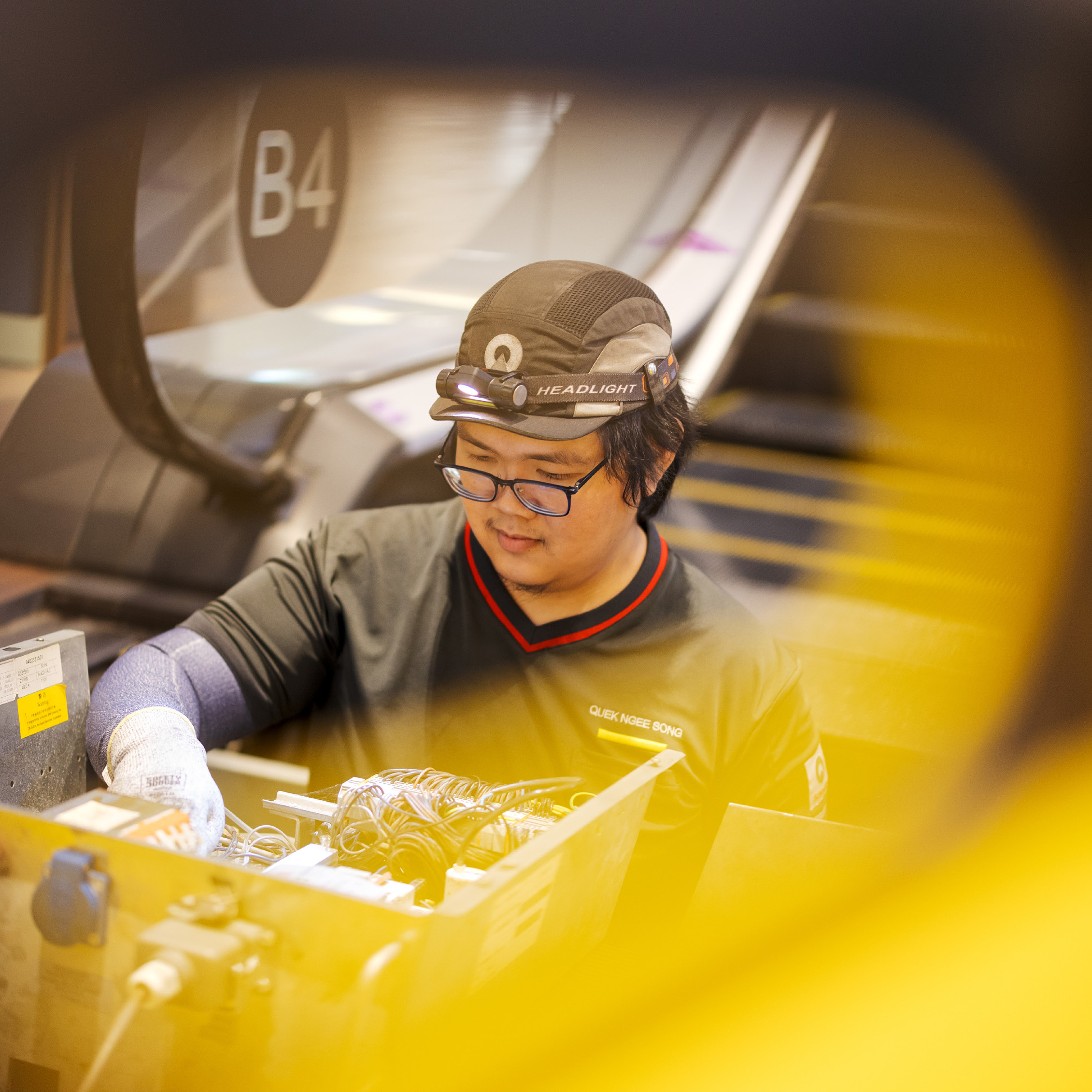
“Our on-site engineers are our most important employees. They determine our success,” says Yeo Wei Liang. “As a service manager, I ensure that they have all the materials they need and support them and make sure they’re okay.” Foo Say Fong, Service Manager of ION Orchard, agrees. “This is a successful approach, as demonstrated by the feedback we receive from our customers,” he says.
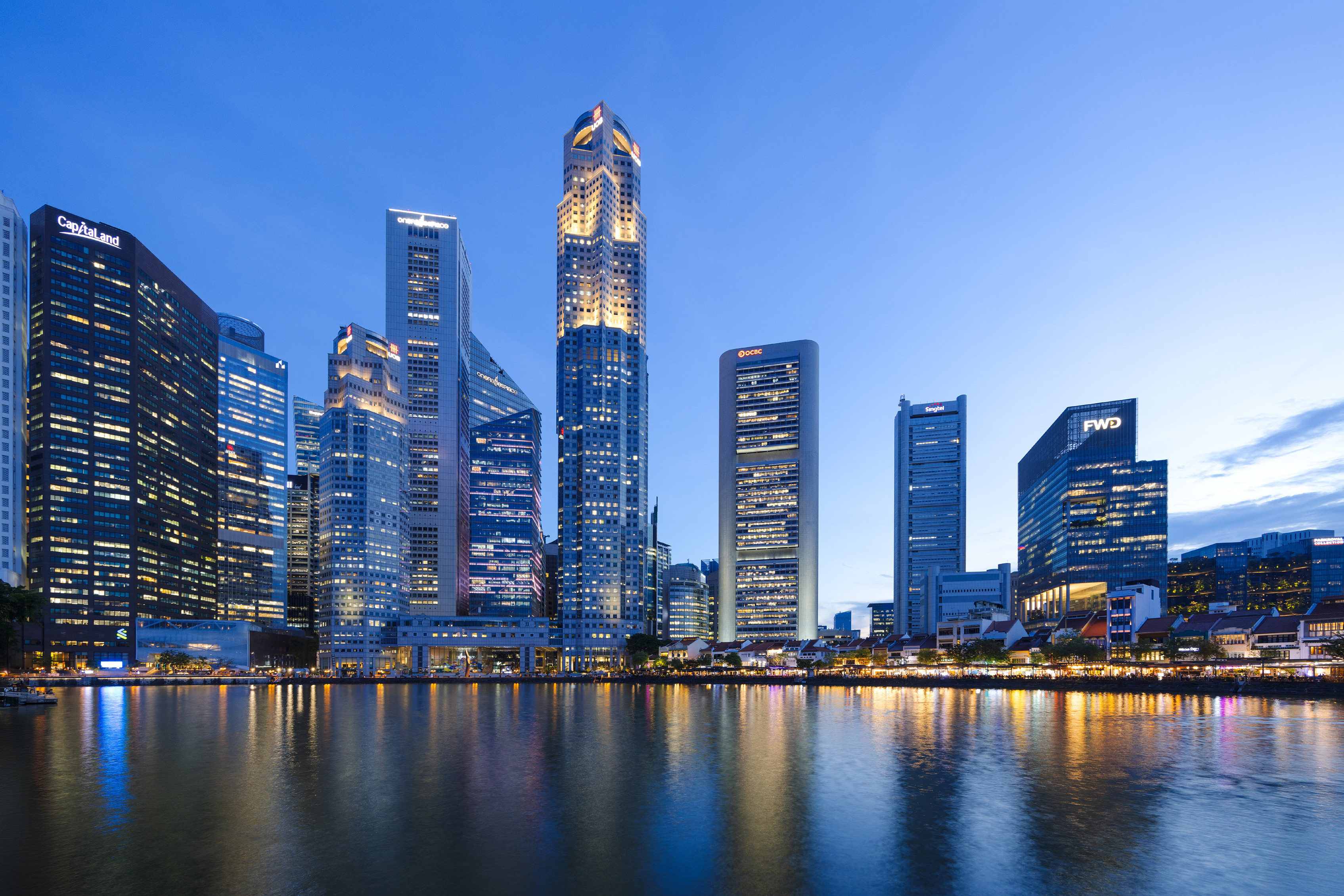
Another prestigious property in Schindler Singapore’s portfolio is the UOB Plaza. The two towers on the banks of the Singapore River date from 1992 and house the headquarters of United Overseas Bank. Here, Schindler modernized the existing 30-year-old elevators and escalators of a third-party provider. In Singapore, there is a large need for modernization – a by-product of the city-state’s history. In 1965, the former British crown colony gained independence before experiencing a construction boom in the 1980s. Many buildings from this era are now aging, and their elevators, which have been in operation for 30 to 40 years, need an upgrade to remain reliable, comfortable, and safe. The modernization process may involve the replacement of individual components such as controls, drives, or doors – or, in some cases, the entire elevator.
“In UOB, we’re modernizing 33 units, and we have already finished work on 32 of them,” says Sekar Kumaraguru, who is overseeing the project. This includes 13 double-deck elevators, which presented the team with considerable challenges. “Working within a very limited amount of space, we dismantled the massive old elevators, each weighing up to seven tonnes, and removed them from the building,” he explains. Schindler 7000 models have now been installed in their place. Terence Lim, Manager Tooling and Resource Center, drew up the technical plans that were needed to hoist the components within the UOB towers. “Lifting heavy components is always a critical point in the process. We need to calculate the lifting points and test them to protect the building infrastructure.”
Modernization projects can take months or years to complete, depending on their scale – all while daily life continues. Schindler Singapore Managing Director Michael Li emphasizes the importance of striking a balance: “On the one hand, we have a very tight schedule. On the other hand, we want to minimize disruption to operations in the building. This requires close coordination and good communication with the customer.” Michael’s been working for Schindler since 2012 and has managed its business in Singapore since 2022. Of the 20 high-rise buildings in the central business district in Marina Bay, eight are equipped with Schindler elevators and escalators. “Each day, we ensure that thousands of employees can travel rapidly and conveniently to their workplaces, to lunch, to appointments, and then back home again in the evening. Schindler units have to operate smoothly to ensure that life in Singapore does not fall out of sync.”
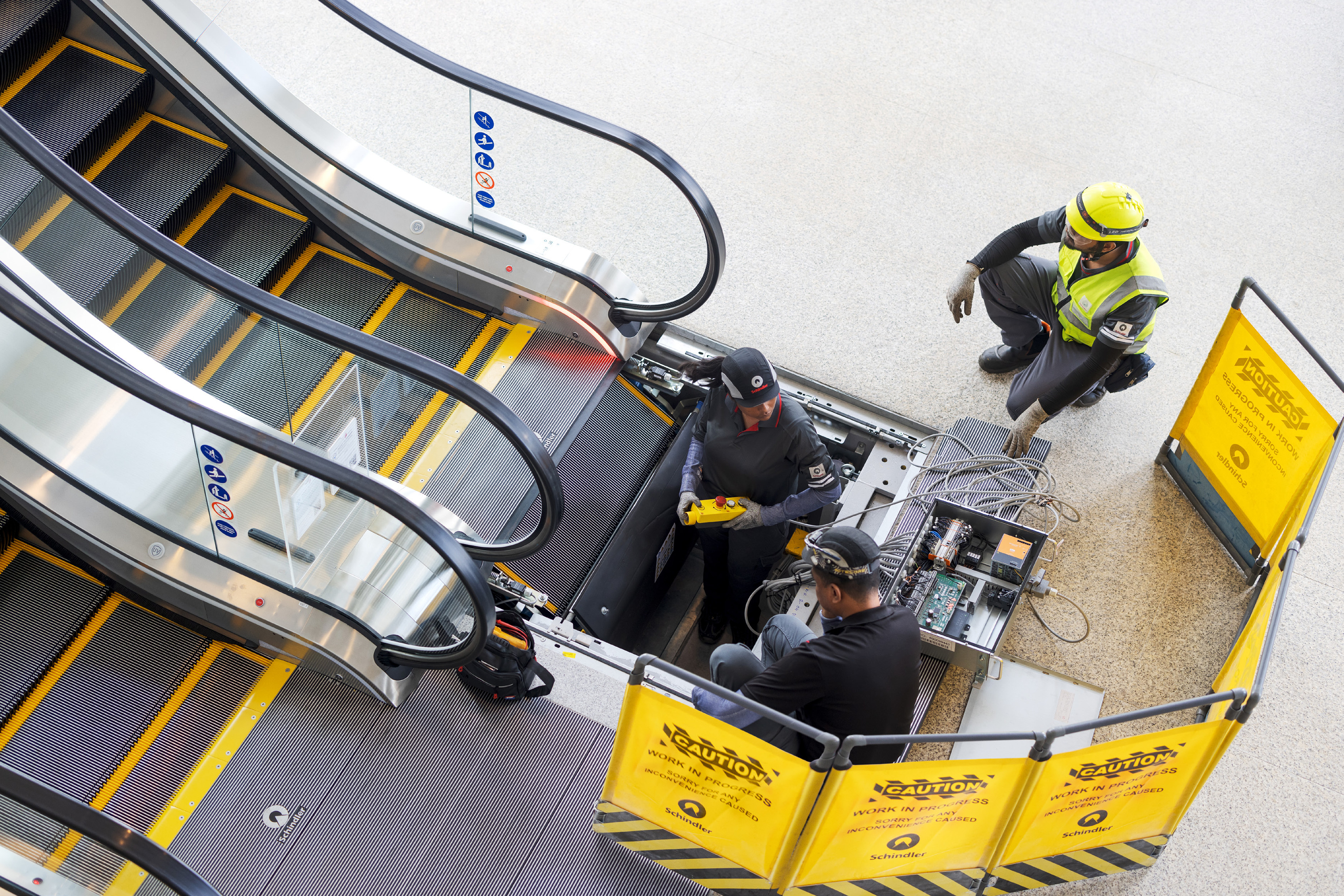