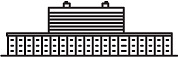
Aarau, Switzerland
A great success
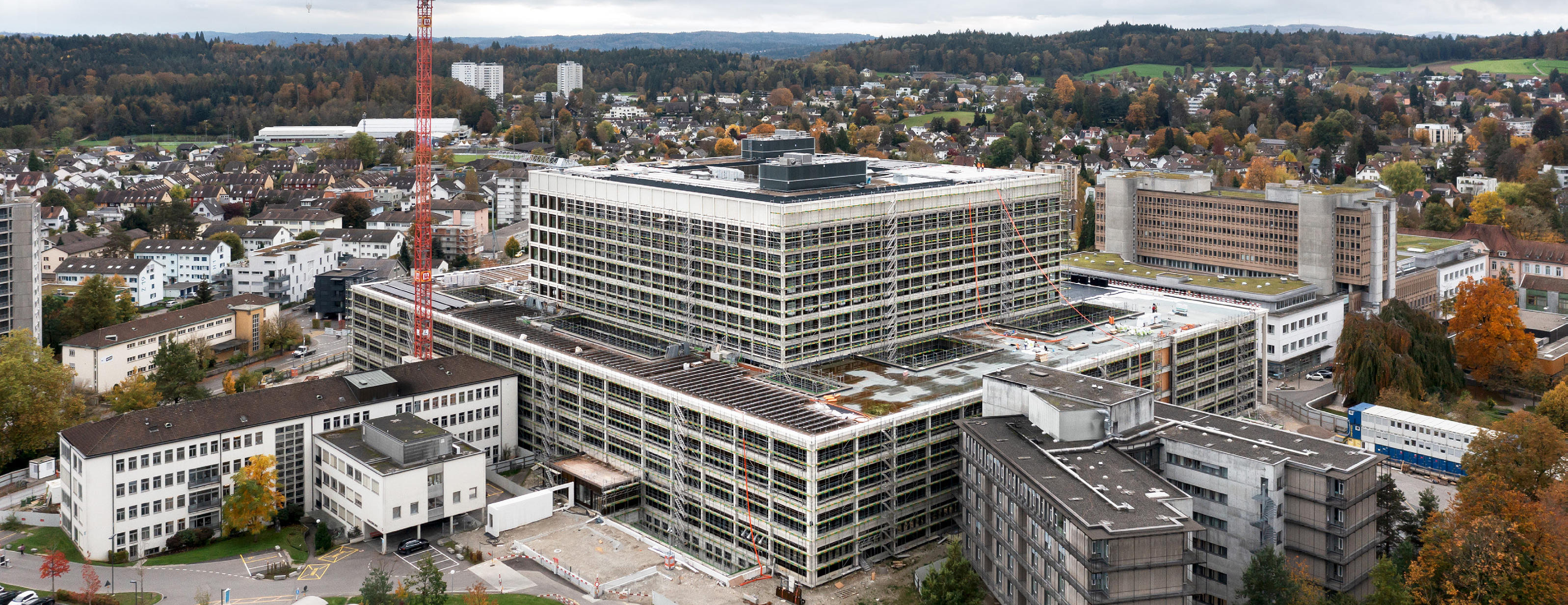
Aarau Cantonal Hospital is getting fit for the future. The “Dreiklang” (triad) project brings together all of the hospital departments under one roof, ensuring short distances for staff and patients – with rapid and reliable connections thanks to elevators supplied by Schindler.
The shell of the new Aarau Cantonal Hospital – or “KSA” for short – is an exemplary construction site. It’s so clean and tidy you’d be forgiven for thinking that staff and patients might be moving in tomorrow. Standing at the foot of the building’s 40-meter façade, Jeannine Graf, Director of Schindler Aarau, is busy talking to Large Project Leader Noel Lauper and Installation Manager Lucien Hasler. Instead of poring over large-scale paper plans, the trio uses a tablet to review 3D representations of the next steps in the construction process. They can even make changes in real time, with these updates becoming instantly accessible to other subcontractors on-site. “Our people are very comfortable using this state-of-the-art technology, and we value the benefits it brings,” says Jeannine.
KSA is one of the first large construction projects in Switzerland to be planned and executed entirely with Building Information Modeling (BIM). During its tendering process, the construction and real estate services firm Implenia made it a prerequisite for bidders to use BIM. This wasn’t an issue for Schindler, a long-time advocate of digital innovation, which eagerly embraced the challenge. Implenia’s Taulant Beqiri, the man in charge of elevators and logistics on the KSA construction site, has been won over by the technology:
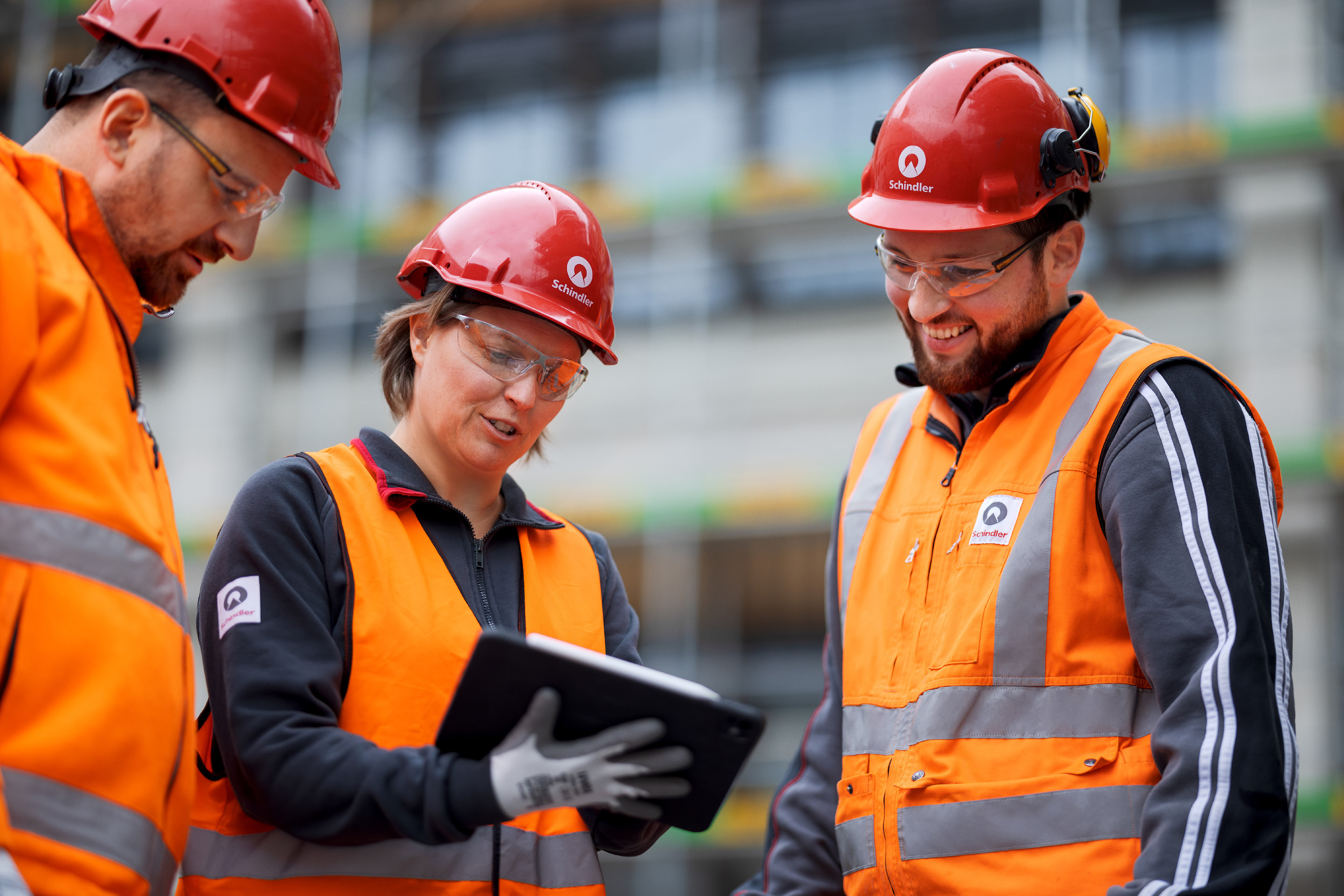
“When it comes to the KSA project, we’re talking about an order volume of CHF 600 million and huge quantities of components and objects. Using BIM means there are fewer errors, and we can clarify open issues digitally, and assign tasks to each other via the system. The information is accessible to everyone and doesn’t get lost. In the past, all of these tasks were carried out by email and on demand.”
Schindler is part of the digital revolution redefining how construction projects are managed. Anna Merkler and Sebastian Müller, Schindler specialists responsible for the deployment of BIM, underscore the advantages of the technology: “Interface planning is much simpler with the digital 3D model.” During project discussions, all participants can move around the model in real time and focus on specific elevators and building elements. Paper plans, on the other hand, make it difficult to pinpoint the exact building level.
In large-scale projects, digital 3D models drastically reduce the potential for errors. “Everyone who’s part of the construction process needs to be involved,” says mechanical engineer Anna. “At Schindler, we want to take all employees forward into this new world, not only the digital natives,” she explains.
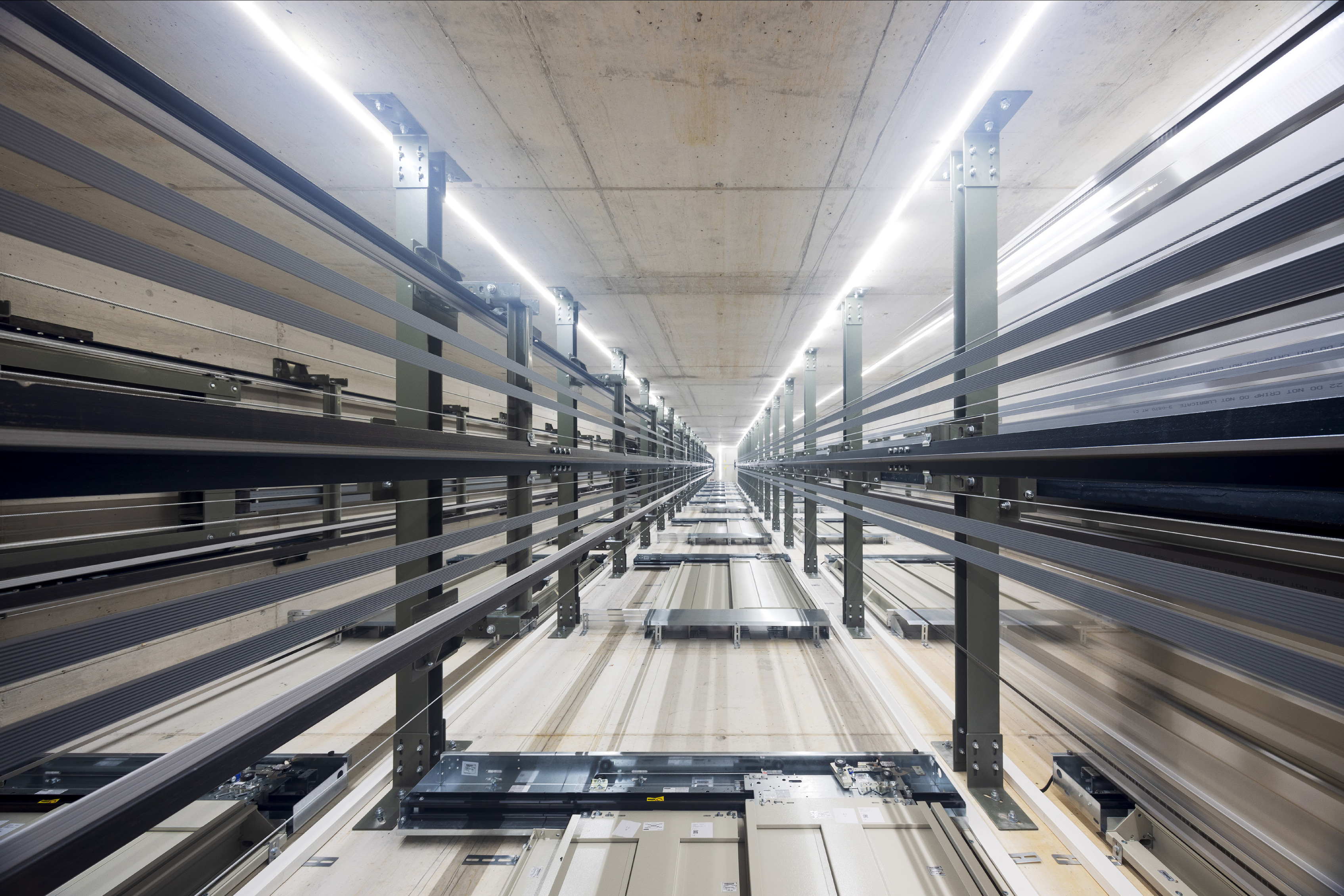
Anna Merkler and Sebastian Müller helped the employees who modelled the 31 elevators for KSA to become more familiar with the new process. “It takes time to adapt to each new planning method,” they explain. These days, large construction firms and the federal government require their partners to use BIM. Beyond offering precise digital 3D models, BIM also provides valuable data that departments like Facility Management can use for operations. This makes BIM an asset not only during construction, but also throughout a building’s life cycle. Anna agrees: “BIM is very helpful across the entire process. We believe in a digital future – none of our customers should have to deal with paper plans going forward.”
Even for Schindler, the scale of the KSA project is remarkable. At any given time, as many as eight installation specialists were busy installing the 29 Schindler 5500 bed and passenger elevators, and two freight elevators. A total of 230 shaft doors were installed, providing different access points to the building – from the basement right up to the two rooftop helipads. Eighteen elevators are equipped with the Schindler PORT transit management system, ensuring smooth and swift transportation for patients and staff while being adaptable to KSA’s future needs. Large Project Leader Noel Lauper comments: “There is a high level of complexity, since hospitals have many more types of users than office or residential buildings. Staff, patients, and visitors all have different access rights, which we can manage very effectively with Schinder PORT technology.”
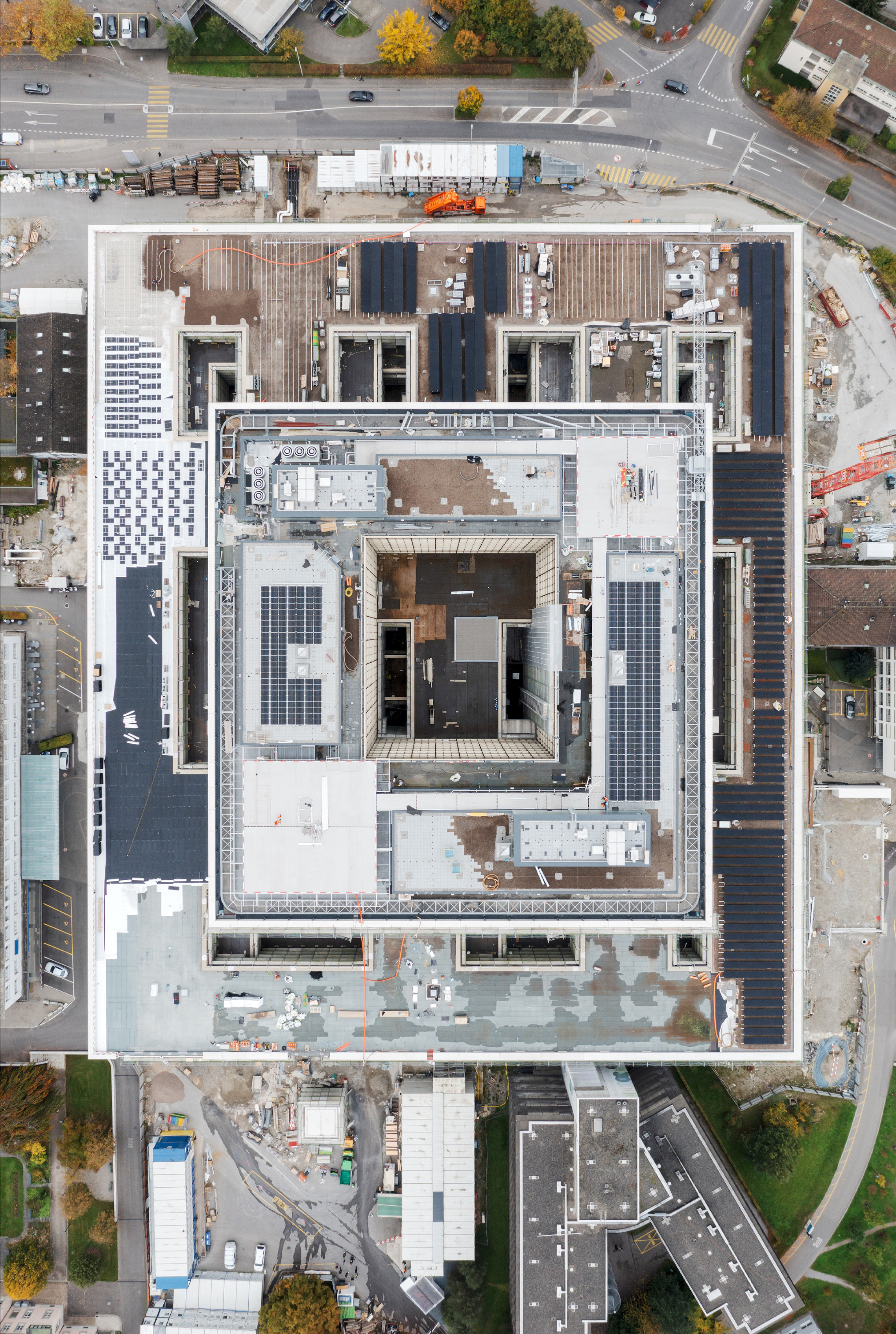
Hospital elevators are complex creatures: they can never be allowed to break down and must be nonmagnetic to accommodate CT and MRI scans, and also need to be shielded against X-rays and reinforced to withstand impact from hospital beds or food trolleys. Maintenance adds another layer of complexity, with special hygiene measures required for elevators serving areas like operating theaters. This is nothing new for Schindler – the 100 employees of the company’s Aarau branch have been performing maintenance on the old hospital buildings for years.
The new KSA, part of the “Dreiklang” project, will house 472 inpatient beds, 130 day clinic places, and 18 operating theaters across 14 floors. Outpatient and inpatient departments are separate, but the building’s design – a four-story base structure topped by a six-story block – minimizes walking distances for staff and patients.
Schindler had from October 2023 to December 2024 to complete the elevator installations. After rigorous two-day testing, each elevator was certified as safe before being handed over to the customer. This step capped off months of meticulous digital planning and seamless collaboration between the parties involved.
Taulant Beqiri explains: “I’ve had the same contacts at Schindler for two years and we trust each other.” He is referring to contacts such as Installation Manager Lucien Hasler. The two men share the same fascination with new builds. “This project is close to my heart,” says Lucien. “Many people will receive the medical attention they need here, and we will have contributed to that. It makes me feel quite humble.”
While digital tools like BIM streamline planning and coordination, bringing those plans to life will always require hands-on expertise – another of the many areas where Schindler employees excel.
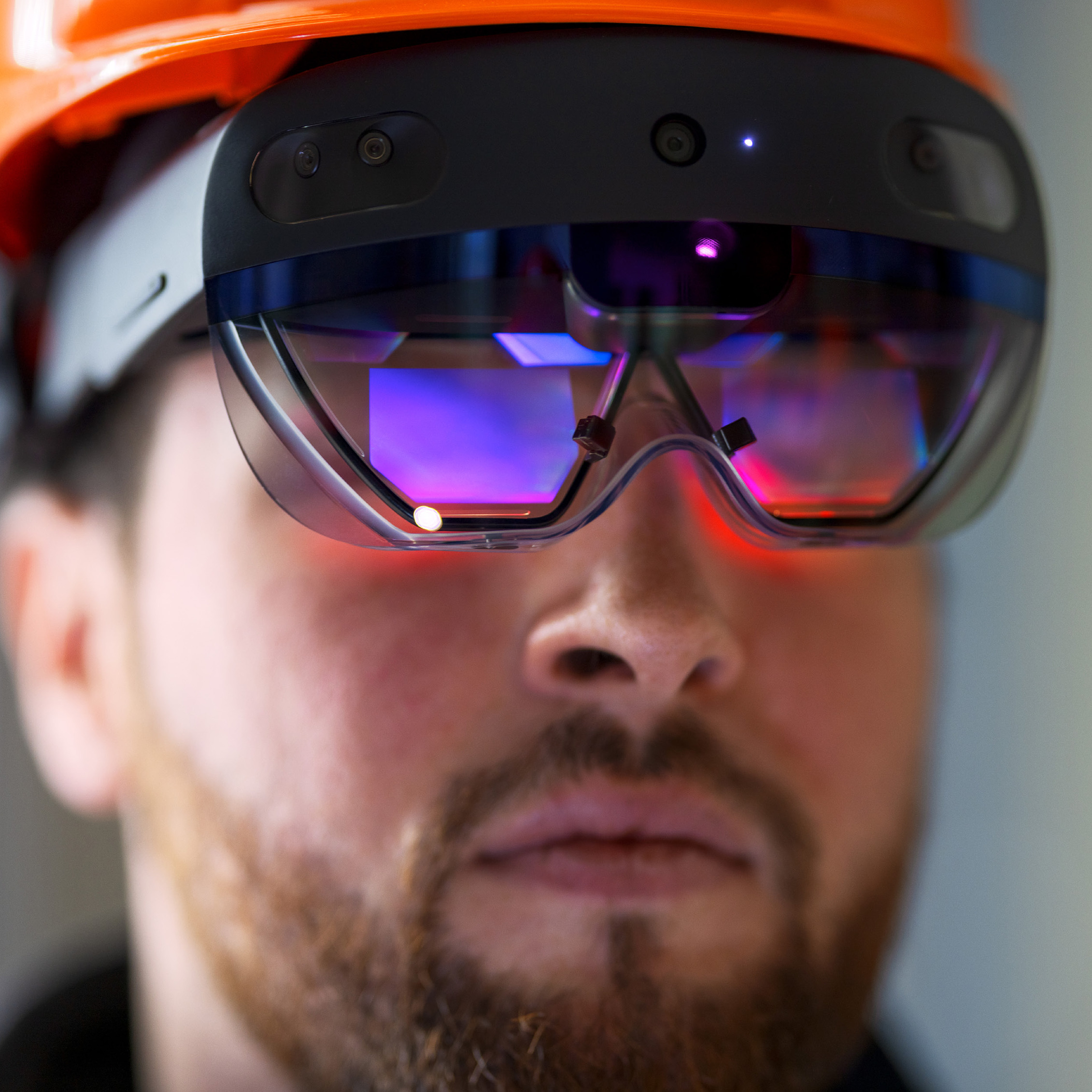
Service professionals
Together, they have 38 years of service at Schindler under their belts. Solving tricky tasks is what they do best.
Hospital elevators have a tighter maintenance schedule because they are used so intensively – up to 1 000 times a day. The average elevator in an apartment block makes just 100 journeys in that time. Not only that, elevators in hospitals are also subject to more wear and tear – such as when a bed or cleaning machine bangs into the doors. If KSA calls for a service technician to deal with a technical issue, Thomas Jander is on the case. He says: “I love finding the source of the problem and then eliminating it. This also means that I’m always learning something new. Keeping critical infrastructure moving is what motivates me day after day.”
Thomas’ boss Daniel Huber is Service Team Leader. He and his team take care of more than 2 000 elevators. The detective work involved in carrying out elevator maintenance also has a particular appeal to him. He does everything he can to ensure that there are minimal service interruptions, and feels well prepared to deal with every eventuality: “We have a very dense network of technicians. We are the only ones to offer this degree of cover.”
The work performed by Daniel’s team will change once the new KSA building is up and running. Until now, the team has been responsible for 50 elevators in the cantonal hospital. However, some of the old buildings no longer exist, and 31 new elevators are being installed as part of the “Dreiklang” project. Once construction is complete, the service team will be responsible for a portfolio of 45 state-of-the-art elevators. And Thomas Jander will be on hand to service those, too.
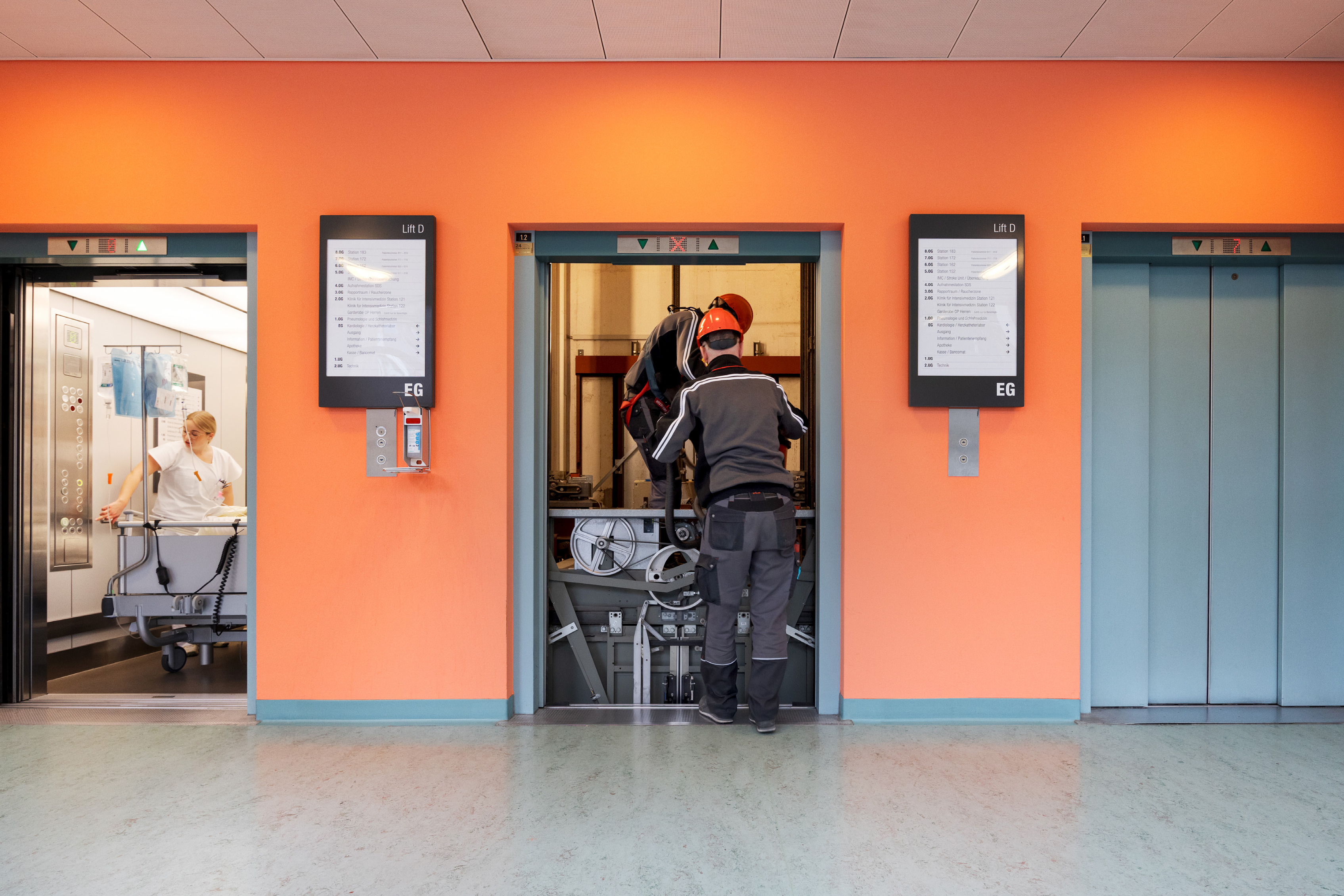
“Exceptional logistics”
The two General Project Managers overseeing the construction of the new KSA are focused on ensuring that this major undertaking goes smoothly and runs like a well-coordinated medical procedure - precise, efficient, and free from complications.
Which aspects of constructing the new “Dreiklang” hospital are challenging?
Nicole Sehringer Bucher: Combining all the departments, which were previously spread across twenty buildings, within one single hospital building.
Bruno Stoll: The sheer size of the building demands exceptional organizational processes and logistics to ensure effective hospital operations.
Coordinating all the different stakeholders on such an enormous construction site is a Herculean task. How do you achieve this?
Bruno Stoll: The total contractor is responsible for this task on the construction site, and our KSA team works closely with them. In doing so, we can minimize friction between hospital operations and work on the vast building site.
What’s attractive about the new hospital building?
Bruno Stoll: Its compactness. And the use of state-of-the-art technologies and high-quality construction methods, in keeping with the Minergie Eco-P standard, that will result in a sustainable building fit for the next 50 years.
How does the “Dreiklang” differ from other new hospital buildings?
Bruno Stoll: According to experts in the hospital construction field, we’re the only ones to have succeeded in developing a hospital that skillfully combines all departments under one roof.
How important is this new building for the region?
Bruno Stoll: Very important. KSA is the largest and most modern cantonal hospital in Switzerland, and one of the biggest employers in Canton Aargau.
Why did you opt for Schindler elevators?
Nicole Sehringer Bucher: At KSA, we’ve had a successful collaboration with Schindler for several decades. Schindler has impressed us with its state-of-the-art technology, and it meets our high standards in vertical transportation.
How important a consideration was the digitalization and sustainability of the elevators in your decision-making process?
Nicole Sehringer Bucher: These were decisive factors. The degree to which logistics are automated has increased significantly with the new building, and elevators are a very important part of logistics processes.
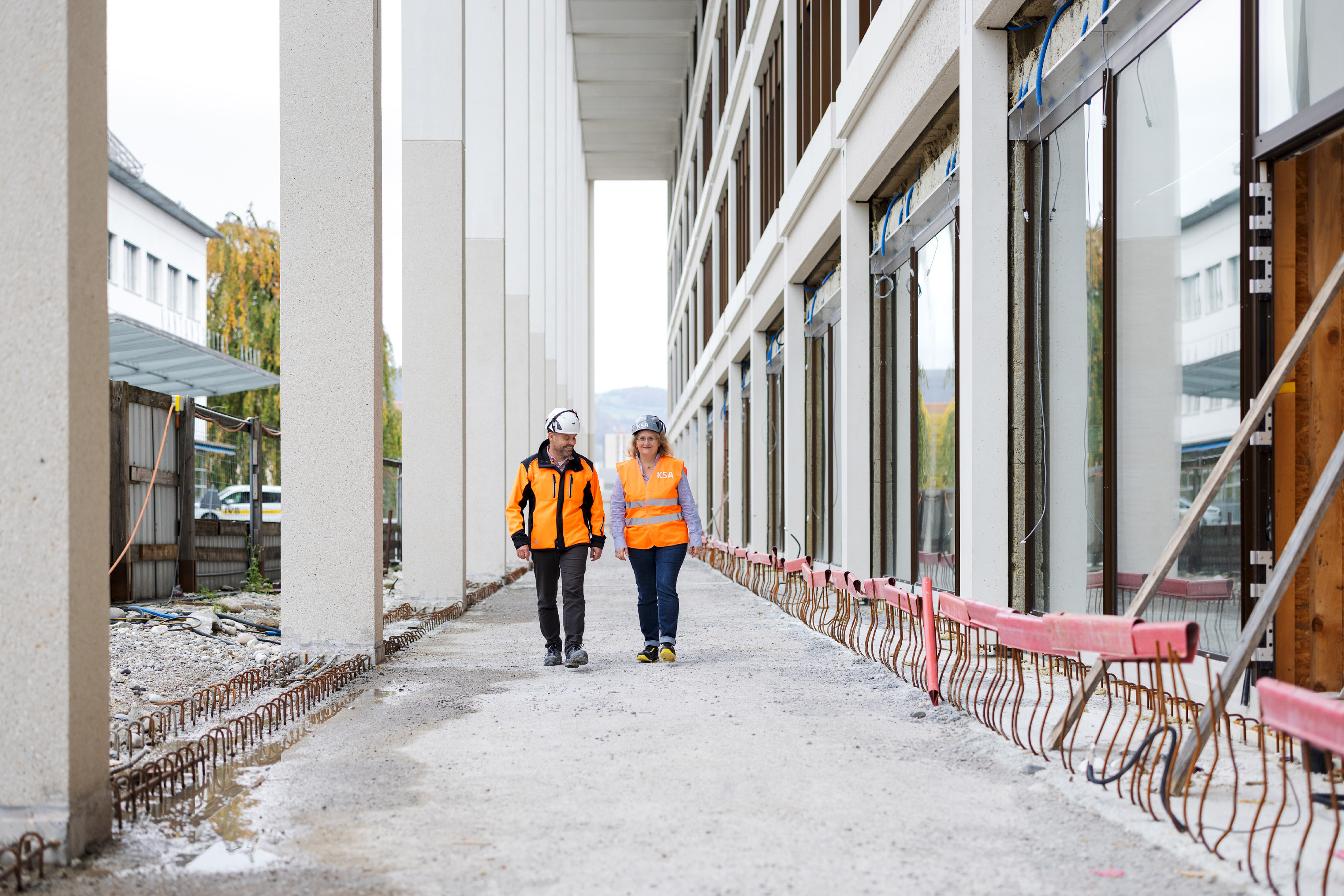