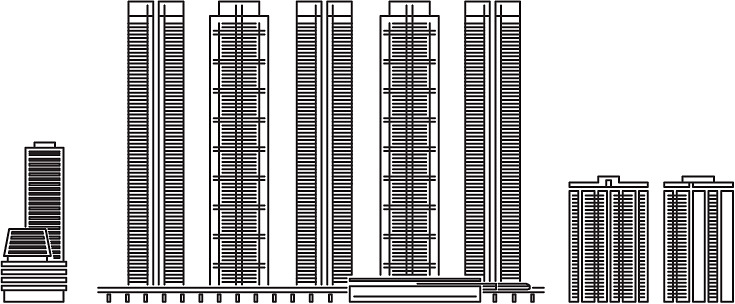
Mumbai and Pune, India
Maximum city
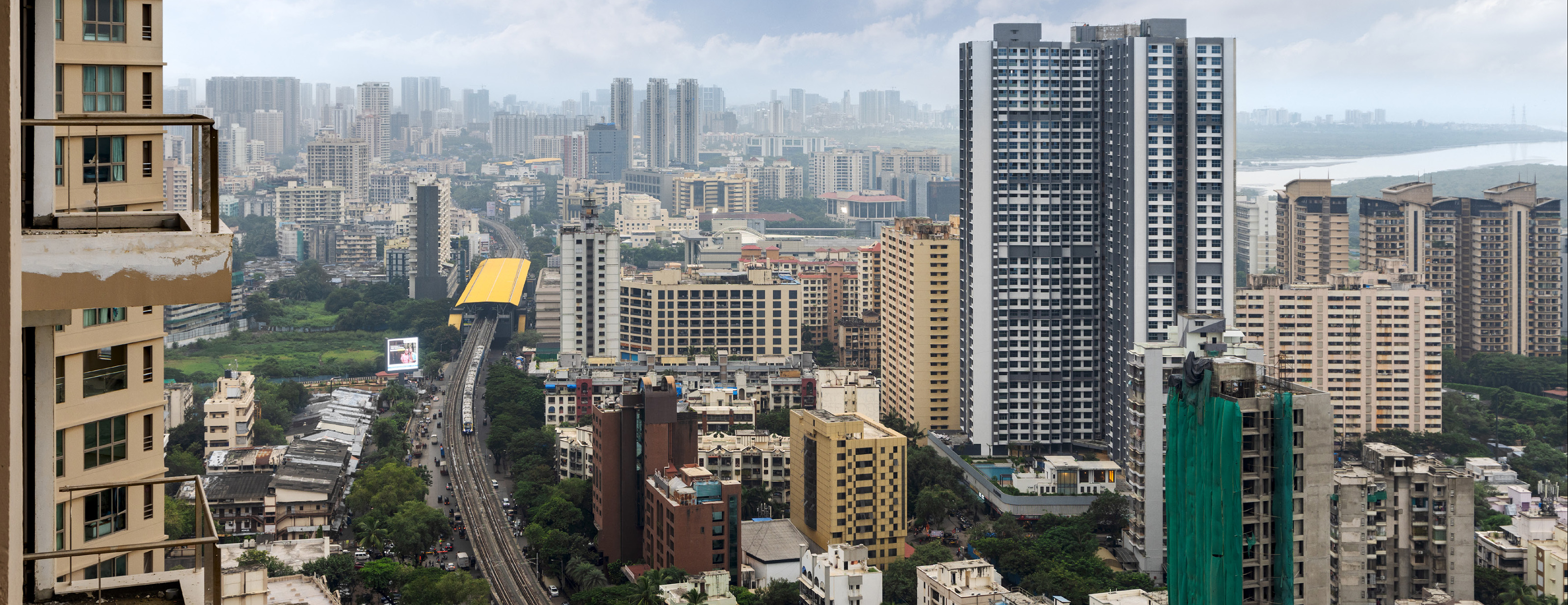
Mumbai’s extensive metro system relies on high-performance Schindler escalators, made in India, to keep passengers moving efficiently through its stations.
Life in Mumbai, a megacity with 13.5 million inhabitants, takes place on two levels. Cars, taxi rickshaws, motorcycles and pedestrians squeeze between and past large concrete pillars at street level. Meanwhile, above them, the spotlessly clean metro darts from station to station on an elevated rail system. The 2A line officially opened almost two years ago, and three metro lines are currently in operation. Everything on the new line is painted yellow – from the roofs of the stations and the signaling system to the trains themselves.
The Mumbai metro is a huge project – construction is taking place in three phases over 15 years. Designed to ease the city’s transport problems, a quarter of the network will be underground, and the rest will run on elevated tracks hosted on pillars that tower above the streets. Once completed, the metro will consist of 16 lines covering a total distance of 357 kilometers and serving 286 stations.
On the 18-kilometer Yellow Line, Schindler has installed 103 Schindler 9700 escalators in 17 stations. This particular escalator model, produced at Schindler’s own plant in Pune, is designed for intense usage and can transport over 200 000 passengers per day.
Today, service technicians Mayur Jadhav and Sachin Rasam are carrying out checks at the Shimpoli stop on this line. They carefully examine the handrails of the six installed escalators to identify any flaws. Routine maintenance work can only be performed at night when the metro is not in use. However, if the Technical Operations Center or metro staff report a problem, the technicians appear on-site swiftly – usually resolving issues in under an hour. This happens between 10 and 15 times a month. Sachin Rasam explains: “We know how important the metro is for the people of Mumbai. The escalators have to run smoothly to allow them to move to and from the platforms easily – and we make sure that’s the case.”
Their checks now complete, the two technicians board the metro heading in the direction of Andheri West, to get to the next station to continue their work.
The Indian government is investing billions in urban infrastructure projects to improve living standards and ease congestion. Schindler India has consistently contributed to projects – like metro systems and airports in Delhi, Bangalore, Mumbai, and Pune – not just by supplying and installing equipment, but also by carrying out maintenance.
In fact, Schindler’s portfolio consists of thousands of units across the country, each one making an average of 700 journeys per year. Tarunesh Mathur, Schindler Senior Vice President Existing Installations Business, explains: “Technical errors can happen; unfortunately it’s not possible to completely prevent them. But we can respond quickly to remedy them if they do occur. We want passengers to feel safe when they use our elevators and escalators – that’s our top priority.”
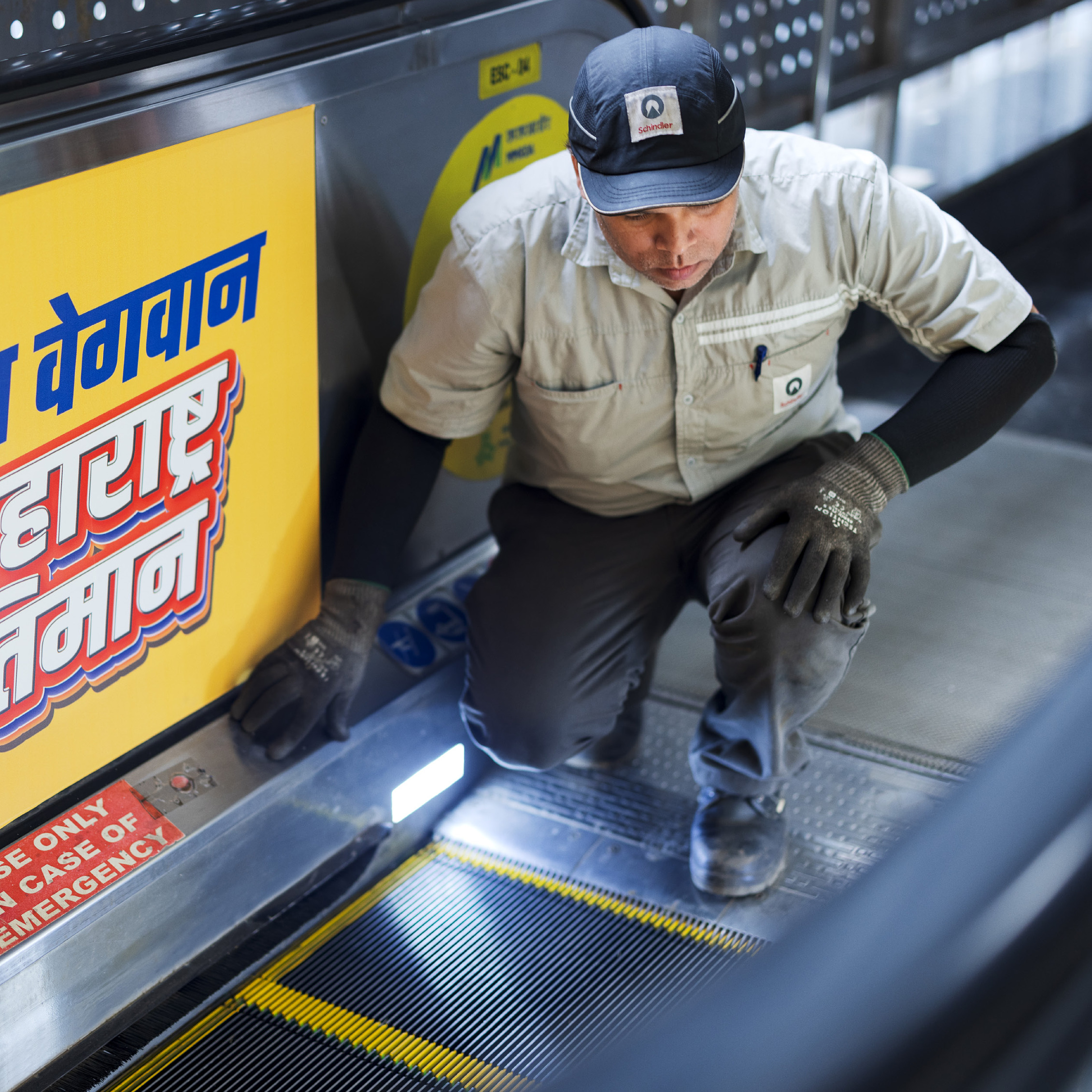
“Swissness comes to our advantage”
How important is the metro project?
It’s a milestone for Mumbai. An efficient public transport network makes everyday life easier and has the potential to reshape a city. Schindler has been involved since the very first phase of this huge infrastructure project, and we’re honored to contribute to enhancing the quality of life for many of the city’s inhabitants. Public transport means easier commuting, fewer cars on the road, and improved mobility for many.
Do you have a favorite project in Mumbai?
I’m proud to say we have the trust of many long-standing customers. I have a very special relationship with the Bombay Stock Exchange, India’s largest. The building is a landmark in our country. Following on from the first modernization of the elevators in 2003, we’ve been entrusted with it again. That makes us proud.
The future for the elevator industry looks rosy in India.
That’s right. We’re in the midst of a societal change. Cities are attractive, especially for the younger population. We need to build upward to meet the new needs of more and more people, so there will inevitably be a growing need for more elevators and escalators. Indians see Schindler products all over the world and have confidence in us when they return from their travels.
What does Schindler stand for in India?
Quality and safety. We exceed the required standards and ensure that everyone, including children, the elderly, and those needing improved accessibility, can travel safely and comfortably. And we maintain active, consistent communication with our customers. Good service is essential for us.
How important is sustainability to you and your teams?
Sustainability is a big focus for us. As of November 2024, 44% of our equipment is ISO Class A. We’ve increased the reach of our digitally connected portfolio and are making significant strides toward gearless systems. We’re also working on initiatives like achieving CII GreenPro certification and making our premises plastic-free. Internally, we’ve engaged employees with activities like the Sustainability Idea Box and various competitions, getting them involved in our journey toward a greener future.
What characterizes Schindler India as an employer?
We’re committed to helping our people grow and succeed. Our consistently high internal employee survey scores show that our people-first approach is working. We make sure our employees feel supported at every step of their careers in this growing economy, through initiatives such as tailored training opportunities, job rotations, apprenticeships, and a strong focus on health and safety.
What is your approach to inclusion and diversity?
We’re very proud to see that our inclusion and diversity efforts are having a real impact. Female representation in our workforce has increased by 30% since just last year – including women in leadership roles. By fostering partnerships with educational institutes, focusing on retention, and creating the right work environment, we’re driving real change – not just at Schindler, but across the industry.
Does it help that Schindler is a Swiss company?
The Swiss are known for their precision and discipline, and people here appreciate that. We’re perceived as a premium brand, and we promote our 150 years of experience and 26 years of operating in India. Experience creates trust.
Sky-high
Oberoi Sky City, an exclusive residential development in the north of Mumbai, features five completed high-rise buildings equipped with 25 of Schindler’s fastest, most elegant elevators.
Mumbai’s skyline has changed dramatically over the last 20 years – just like the city itself – with high-rise buildings now a dominant feature. Real estate developers like Oberoi have taken the luxury residential property market by storm.
The five 200-meter-high towers of Oberoi Sky City in Borivali East form a zigzag silhouette. The complex, which features a shopping mall, a hotel, and more than 1 500 apartments, took five years to build, and officially opened three years ago. It’s located within walking distance of a metro station, making it easy for residents to travel around Mumbai, a city renowned for traffic congestion.
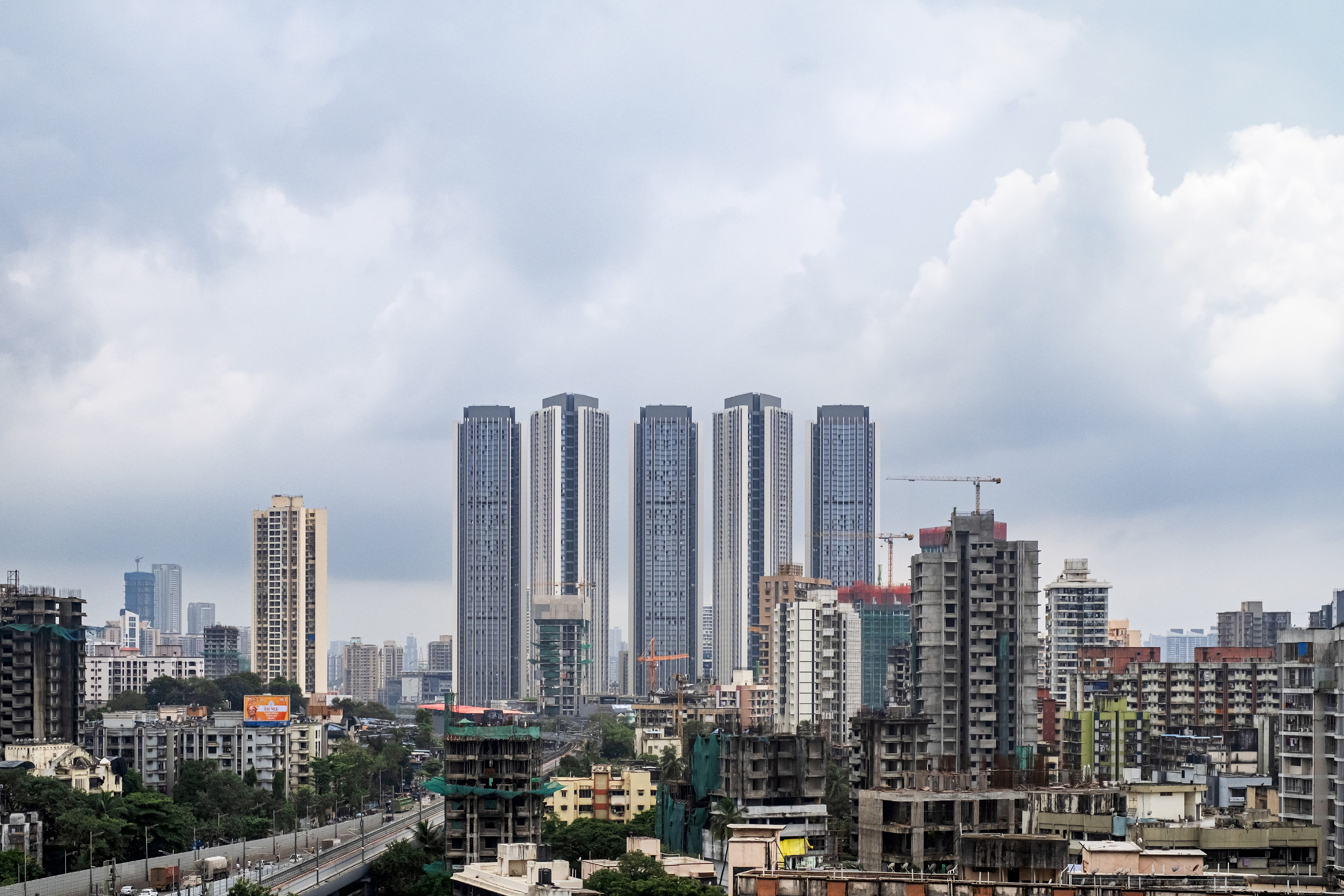
Within the complex, the 25 Schindler 7000 high-rise elevators, each fitted with the Schindler PORT transit management system, serve all 62 stories, whisking residents to their destinations at an impressive five meters per second. Six additional elevators serve the lower levels. All the elevators are connected to the Schindler Technical Operations Center, enabling immediate detection of any irregularities. Schindler will also supply 32 escalators for the upcoming Sky City Mall.
The collaboration between Schindler and Oberoi builds on years of trusted partnership, with the real estate developer sourcing elevators and escalators exclusively from the Swiss company, which has local production facilities in India. “Oberoi has very high standards and expectations regarding quality, exclusivity, and the products they want. Its owner, Vikas Oberoi, chose to work with Schindler, and we’re committed to demonstrating our expertise day after day,” explains Schindler Area Manager Existing Installations Arun Meneze.
India has emerged as a thriving economic powerhouse, with a young, qualified population with high quality-of-life expectations. Cities are expanding skyward, while massive infrastructure projects transform local public transport systems and connect urban districts. Like other cities, Mumbai, a city bordered by sea on three sides, faces a simple geographic reality: the only way to grow is up.
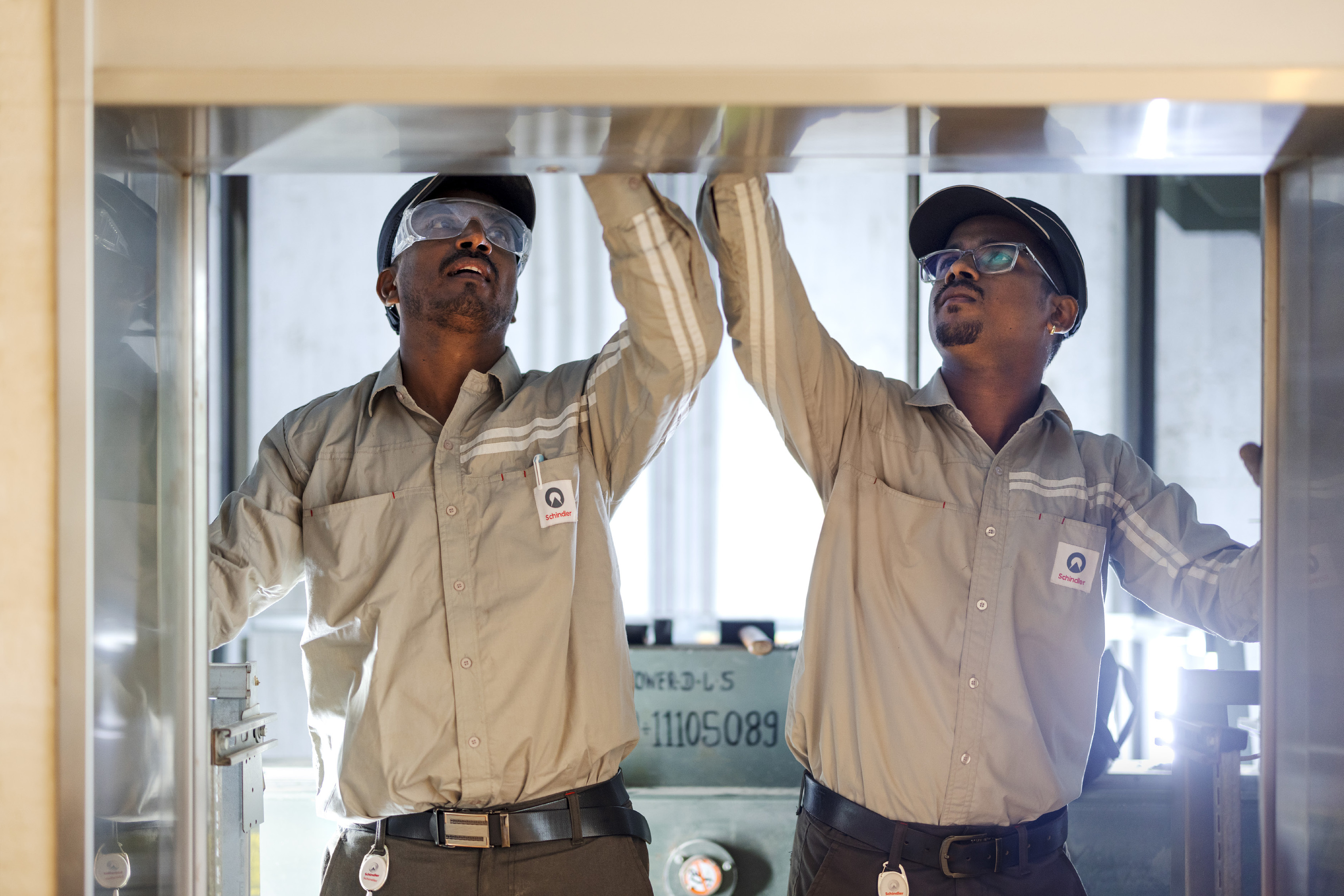
One of the top ten globally
The Bombay Stock Exchange (BSE), one of the city’s landmarks, is getting a cutting-edge elevator upgrade – its second modernization by Schindler since 2003.
With a trading volume of USD 5 trillion, the BSE ranks as one of the world’s top ten stock exchanges. Located in the historic heart of Mumbai, on Dalal Street, the 29-floor building has dominated the skyline since 1980, and is a symbol of the subcontinent’s functioning economic and trading system. Schindler’s relationship with BSE began in 2003 when it modernized the building’s eight elevators, which it has continued to service ever since. These elevators are now undergoing a comprehensive upgrade. To minimize disruption to the building’s daily operations, the modernization is being carried out in phases. Schindler engineers are installing Schindler 5000 elevators integrated with the Schindler PORT transit management system. This enhancement will significantly improve mobility throughout the building for employees and visitors alike. The project is due for completion in two years.
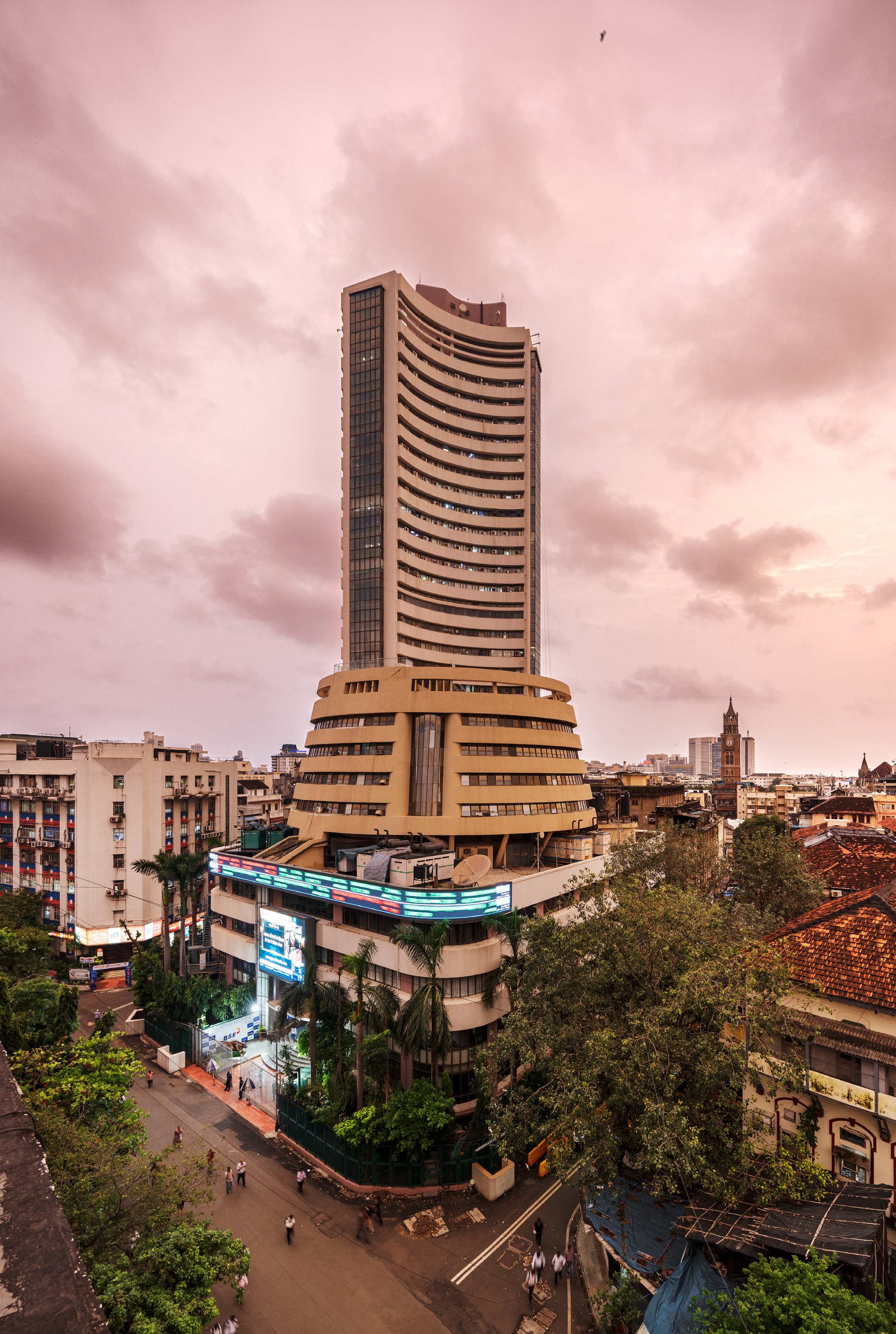
Homemade
From its plant outside of Pune, Schindler builds elevators and escalators for the whole subcontinent – delivering Swiss quality, made in India.
White plastic covers gleam in the sunlight. They protect the escalator steps currently lying in front of the assembly hall, awaiting collection. Soon, they’ll be installed in shopping malls and metro stations, helping customers to access shops and passengers to catch their trains.
The Pune Chakan plant is Schindler India’s pride and joy, hosting 1 200 employees. In one of its two massive factories, employees have been producing elevator components since 2014. In the other, specialists, among them 48 women, have been building escalators since 2018. An R&D unit was added in 2016, and the following year, managers launched a Schindler university here.
The company had only just established a presence in India 26 years ago when it began investing in its own elevator and escalator production. And it didn’t take long for the Schindler brand to be noticed. The company was able to offer Swiss-quality products that met international standards while being manufactured locally and tailored to the needs of the Indian market. Nitin Chalke, Head of Schindler India, says: “Other companies wait 40 or 50 years before making such a large investment in India. We were bold and invested quickly.” Bold because with the advantages of being first also come the risks. But the approach paid off – and the plants were soon working to capacity.
When deciding where to establish the Schindler campus, nothing was left to chance. Pune is 150 kilometers from Mumbai – which is the country’s largest port – and is home to a thriving industrial sector, with a particularly successful car industry, helpful when it comes to finding suppliers who can meet Schindler’s specific needs. There’s also a large pool of engineers in the city. Every year, 200 000 students graduate from 60 engineering colleges and look for work. Schindler’s R&D and training center, along with the opportunities for employees to put their learned skills into practice in elevator and escalator production, make it an appealing option.
Anuj Datta, Head Supply Chain at the Pune plant, says: “Here in Pune, we can produce every type of Schindler elevator and escalator. That’s something our employees are very proud of. We’ve added the Schindler 1000 elevator for the more affordable housing segment to our range, which reflects our ambition to grow our overall market share.”
In one of the Pune campus factories, engineers and mechanics use smart machines and advanced robotics to produce components for established Schindler elevator lines. Each elevator produced on-site is assembled, tested, then dismantled into individual components that are then carefully boxed for safe delivery.
Each new elevator series undergoes quality controls in Pune before being approved and dispatched to customers, within India and out to Sri Lanka, Myanmar, and Bangladesh. Twice a week, the internal control team takes out the components that have already been packaged and assembles an elevator to identify any possible defects. Nimish Deshpande, Head R&D India, explains: “We test every type of elevator software here in Pune before it’s approved for use. We also work with mechanics, electricians, and software engineers to develop components for specific product lines – not just for India but for the global market. Cabins for freight elevators are just one example.”
Three key components for all Schindler elevators worldwide are produced in Pune. Elevator belts are made from synthetic polymers and cables, examined under the microscope and checked for tensile strength, before being cut and packaged. Brake blocks for elevators are welded by on-site specialists while doors are folded into shape by high-speed robots.
The second large factory where escalators are produced is located in the north of the campus and covers an area of 200 000 square meters. Sun streams into the building through multiple skylights, bathing the construction teams in light as they work shifts on two production lines, assembling escalators and preparing them for dispatch.
The Pune campus was built according to the latest environmental criteria and was subsequently awarded the IGBC Gold Rating (equivalent to LEED certification) in recognition of its green building credentials. Today, 35% of its energy consumption is provided through solar power, with the goal to increase that figure to 70%. Schindler India is also seeking to halve its CO2 emissions by 2030, by using more energy-efficient machines to process metal, enhancing vehicle capacity and reducing packaging waste – practices that are also encouraged among suppliers. Canteen and garden waste is composted on the campus and then reused, providing nutrients for the campus’ fruit and vegetable gardens. Homemade all the way.
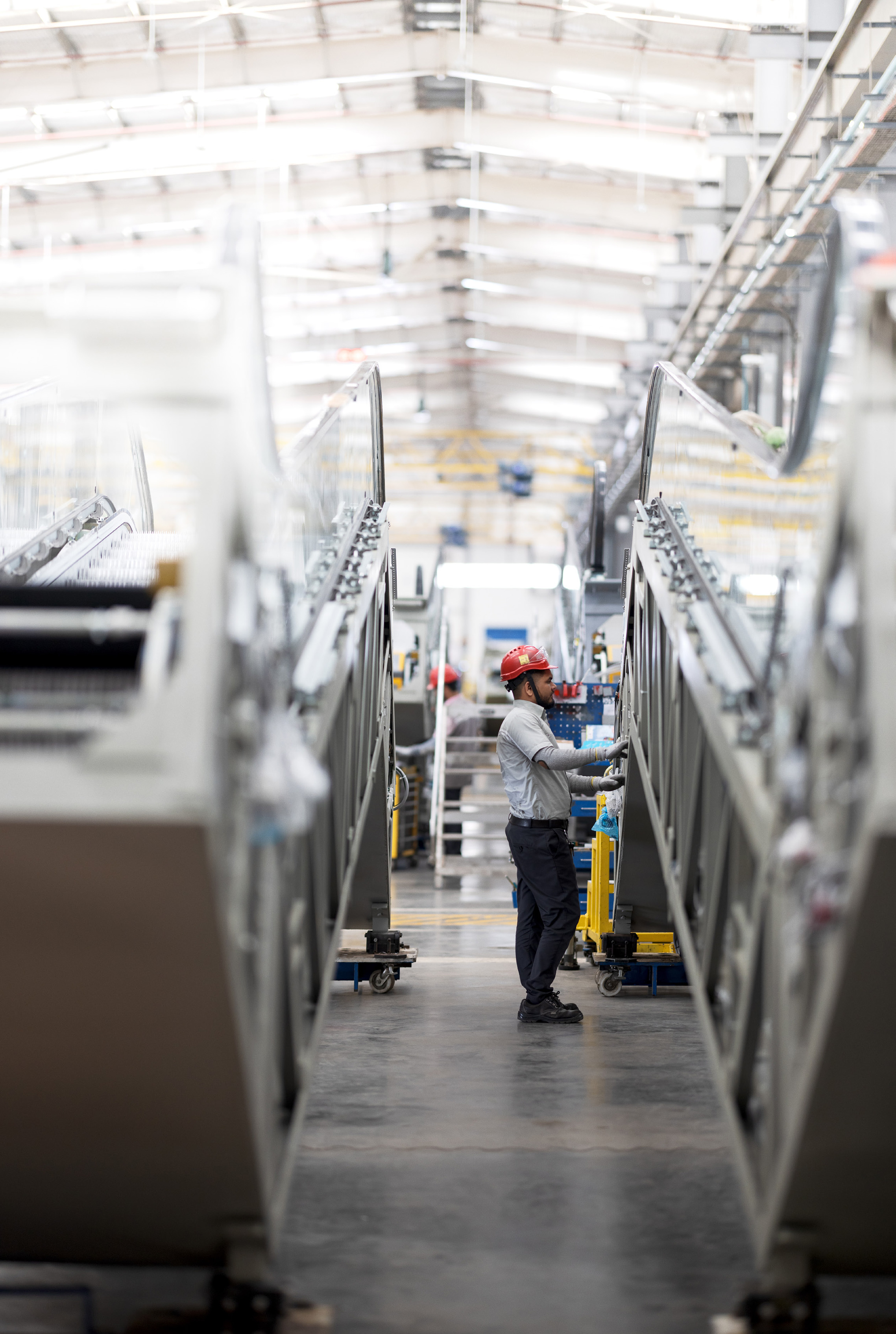
All for one and one for all
The Business Shared Services Center handles the administrative tasks for all Schindler India branches, streamlining operations and enabling agility. In her leadership role, Vice President Vijayakumari Krishnamurthy prioritizes employee working conditions and consciously deconstructs societal norms.
The second floor of the Pune factory premises comes alive with the hum of computers and the click of keyboards. Here, at any given time, contracts for new installations are drafted, professional aspirations take shape, service agreements are finalized, and financial reports are written. Since 2021, the Business Shared Services Center (BSC) has centralized the administrative activities of 40 Schindler branches across the country. Beyond its core functions, the BSC has made employee engagement, career development, and cultivating a positive work culture top priorities.
What stands out on first glance is the large proportion of women in the office – around 40% of the BSC workforce, a relatively high percentage for the country. As Vijayakumari Krishnamurthy, who’s been in charge for the past year, explains: “India is a country with strong traditions. Things are changing, but many people – especially women – can only partially participate for fear of violating conventions. We want to address this, and so we’ve created an environment in which women can feel comfortable.” Schindler’s Yashaswi program, named from the Sanskrit word for fame or victory, lays the foundation for women to combine societal and family norms with their professional ambitions, and supports them in every phase of their lives. The company provides bus transfers for female employees, to ensure they can safely travel to and from work, and allows women to work from home during their menstrual periods. The program also includes meals, safety training, and free hygiene products, and a taxi transfer service for pregnant employees.
Beyond the BSC, the needs of female employees are top of mind across Schindler India. For example, protected spaces and separate toilets are provided for female installers and service technicians on construction sites. And, as Head of Schindler India Nitin Chalke comments: “This is just the beginning. We want to be an attractive employer for the growing pool of female talent.”
Looking ahead, the BSC team plans to focus on further implementing automation technologies to boost efficiency, refine processes to enhance scalability – and of course continue fostering greater diversity and inclusion.
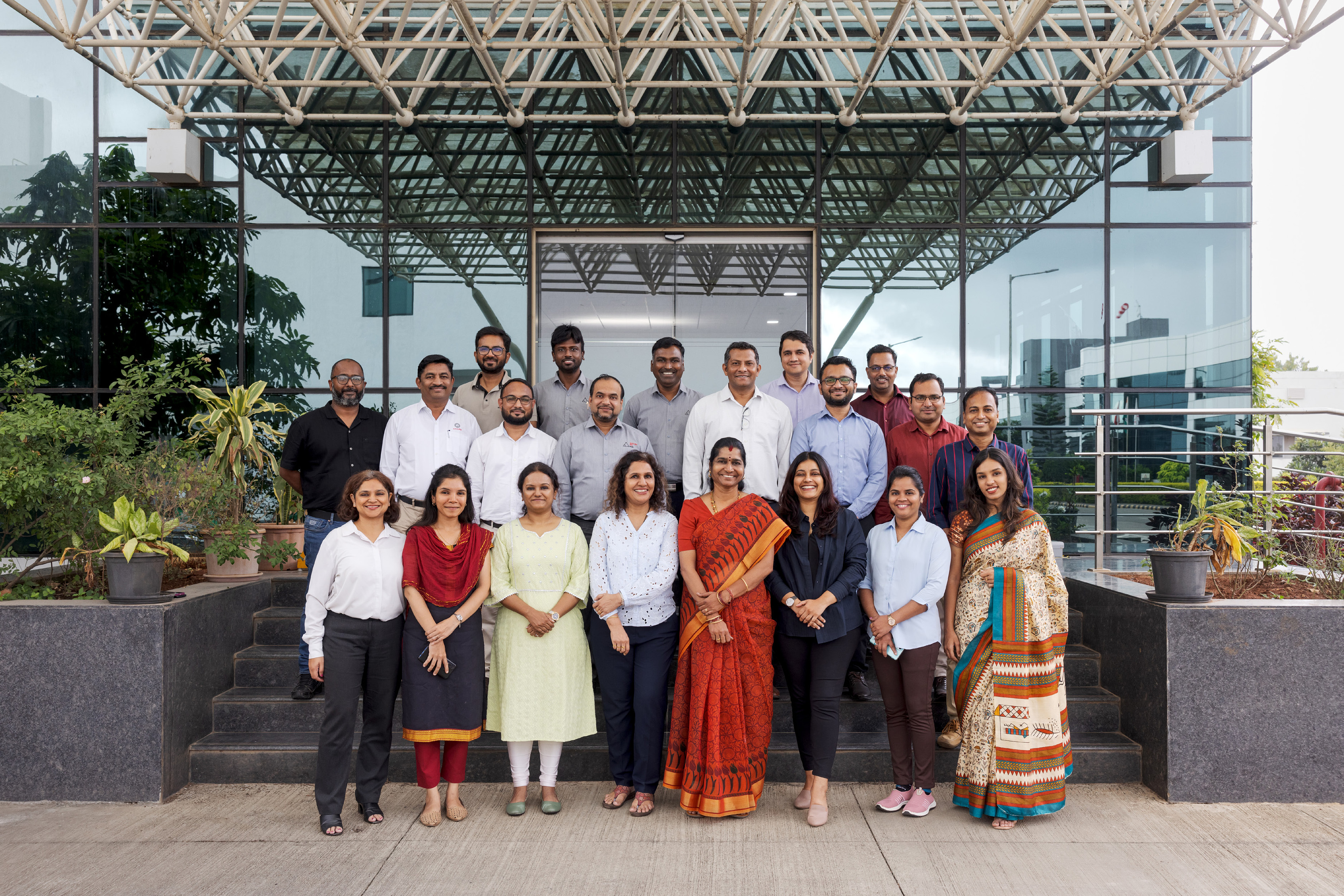
A city within a city
From utopia to reality: Nanded City was established in 2010 by owner and director Umesh Magar, who had a vision to create a unique living space.
Umesh Magar, why did you establish Nanded City?
We wanted to create a living space that meets the latest environmental standards and provides a state-of-the-art school system and modern working conditions, all within a safe and secure environment. In other words: a contemporary city where people want to live.
What was your personal motivation?
We wanted to give something back to society.
What makes Nanded City so attractive?
The fact that it’s so green! We planted 20% more trees than the state requirements and that really had an impact. It’s also a safe area where people go out for walks, not just during the day, but also at night.
Why has no one copied your concept yet?
Honestly, I don’t know. I’ve already exchanged ideas with the Prime Minister and various state governors.
Why did it work for you?
People believed in us, and we proved our loyalty. My uncle, a politician, enjoyed high trust among the people.
Why do you trust Schindler as a partner?
When it comes to Schindler, we’re pleased with the quality the company delivers, and with our ongoing collaboration. We’re committed to working with our partners long term.
How involved are you in the day-to-day work and organization?
If I see that something isn’t working, I immediately do something about it. People can’t live without elevators nowadays. We therefore need to have a good, reliable product – one with a long lifetime and minimal downtime – not to mention swift customer service.
The scale of this community outside Pune is impressive, with 192 residential blocks for 40 000 people and 11 000 generously sized residential apartments. It’s also home to an IT park, a shopping mall, sports facilities, a hospital, and schools. Clean sidewalks and round-the-clock CCTV monitoring create a welcoming and secure environment for all. Nanded City is a city within a city, shaped under the vision of Umesh Magar and his family.
Reena Ganatra, Schindler General Manager in Pune 1 Branch Office, says: “Umesh Magar is one of our biggest customers, and our relationship with him is very important to us. He sometimes calls me at 7 a.m. and I’m there for him. That’s the level of service we offer.”
Schindler takes care of a portfolio of 285 elevators and 4 escalators in Nanded City. Seven service technicians work on-site to ensure all the elevators operate smoothly at all times. One of them is Satish Sampatrao Bhojte, a veteran Schindler employee with 14 years under his belt. He says: “I sometimes get thank-you cards from the customer. He’s satisfied with our work.”
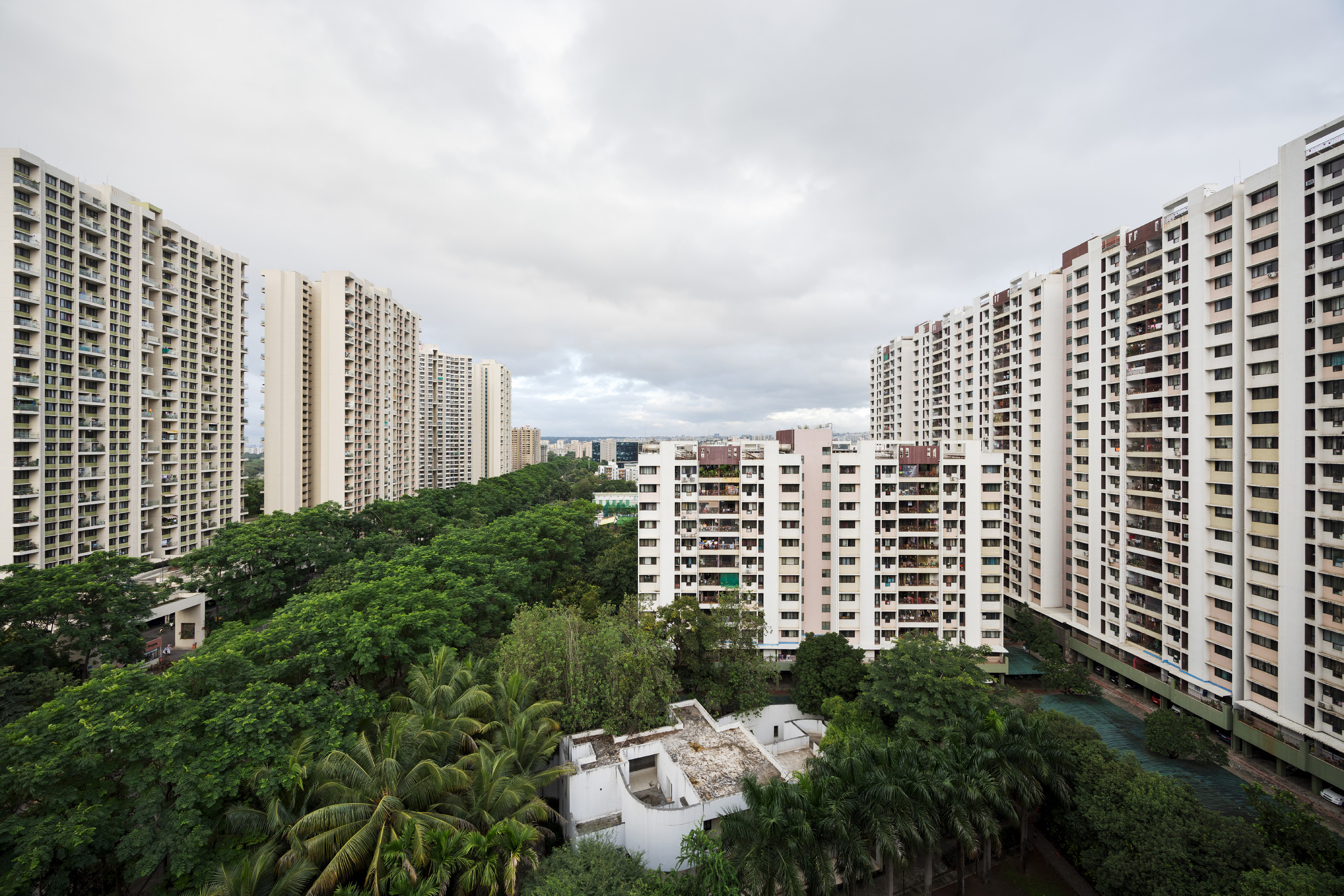